Hydraulic Equipment Casting: Understanding the Process and Benefits
Hydraulic equipment casting is an essential process in the manufacturing industry. It involves creating complex shapes and designs for hydraulic components that are used in various applications, including automobiles, aerospace, and construction. The process of hydraulic equipment casting involves pouring molten metal into a pre-engineered mold that creates a specific shape or form.
The use of hydraulic equipment casting has become increasingly popular due to its ability to produce high-quality, complex parts in large quantities. The process allows for the production of intricate designs that would be difficult or impossible to create using other manufacturing methods. Hydraulic equipment casting is also cost-effective, as it reduces the need for additional machining and finishing processes. As a result, it saves time and money while increasing efficiency in the production process.
Overview
Hydraulic equipment casting is a manufacturing process that involves the production of hydraulic components through the use of casting techniques. This process is widely used in the production of hydraulic cylinders, pumps, valves, and other hydraulic components.
The hydraulic equipment casting process involves the use of a mold into which molten metal is poured. The molten metal is then allowed to cool and solidify, taking the shape of the mold. This process is used to create intricate shapes and designs that would be difficult or impossible to produce using other manufacturing methods.
The hydraulic equipment casting process is used to produce components that are strong, durable, and resistant to wear and tear. The components produced through this process are used in a wide range of applications, including construction, mining, agriculture, and manufacturing.
The hydraulic equipment casting process can be used to produce components in a variety of materials, including aluminum, brass, bronze, iron, and steel. The choice of material depends on the specific application and the properties required of the component. For example, aluminum is lightweight and corrosion-resistant, making it an ideal choice for hydraulic components used in marine applications.
In summary, hydraulic equipment casting is a widely used manufacturing process that produces strong and durable hydraulic components. This process allows for the production of intricate shapes and designs that would be difficult or impossible to produce using other manufacturing methods. The choice of material depends on the specific application and the properties required of the component.
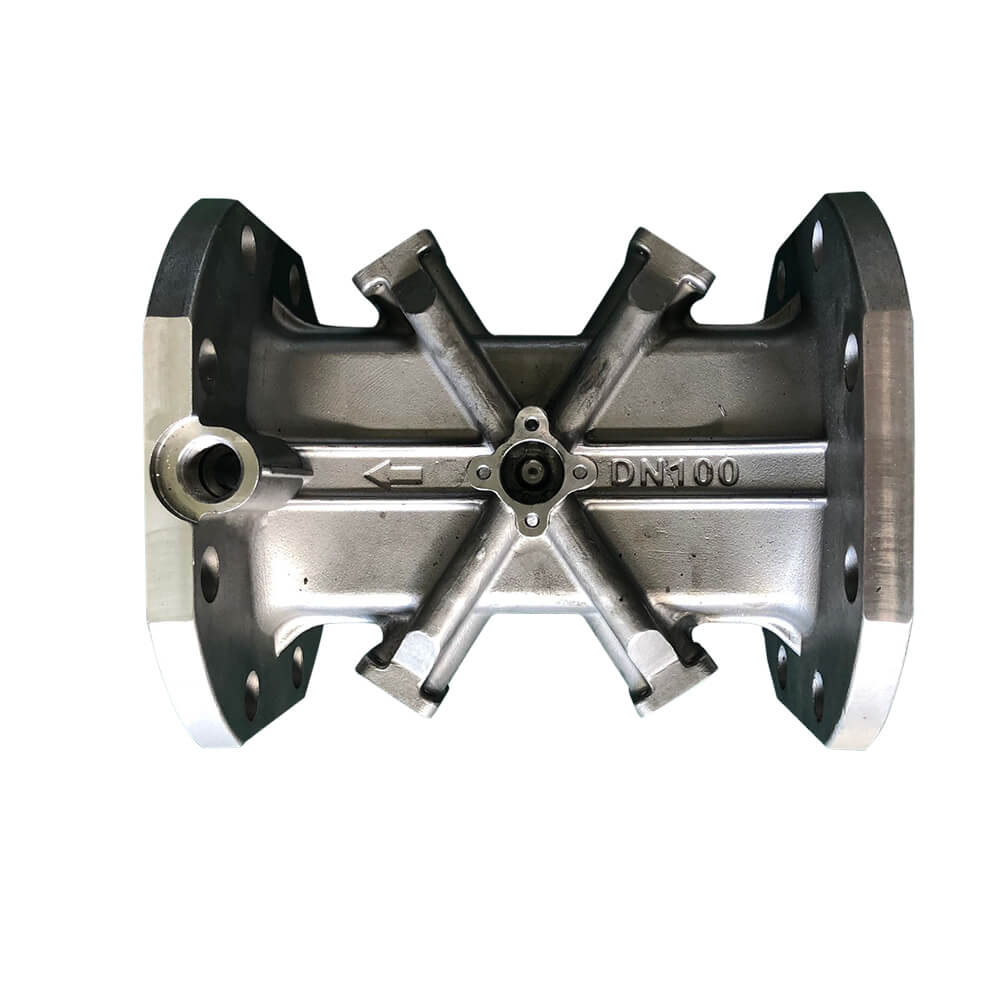
Benefits of Hydraulic Equipment Casting
Hydraulic equipment casting is a manufacturing process that involves pouring molten metal into a mold to create a hydraulic component. This process has several benefits that make it a popular choice for producing hydraulic parts.
1. High Precision and Accuracy
Hydraulic equipment casting allows for the creation of complex shapes with high dimensional accuracy. The molds used in this process are made with precision and can be designed to produce parts with tight tolerances. This precision ensures that the hydraulic components fit together perfectly, reducing the risk of leaks and other issues.
2. Strong and Durable Parts
Hydraulic equipment casting produces parts that are strong and durable. The process involves pouring molten metal into a mold, which creates a solid and dense part. This density makes the parts resistant to wear and tear, ensuring they last longer and require less maintenance.
3. Cost-Effective Production
Hydraulic equipment casting is a cost-effective way to produce hydraulic components. The molds used in the process can be reused multiple times, reducing the cost of production. Additionally, the process allows for the creation of complex shapes in a single step, reducing the need for additional machining and labor costs.
4. Versatility
Hydraulic equipment casting is a versatile process that can be used to produce a wide range of hydraulic components. The process can be used with a variety of metals, including aluminum, copper, and steel. This versatility makes it a popular choice for producing hydraulic parts for a variety of industries, including aerospace, automotive, and construction.
In conclusion, hydraulic equipment casting is a reliable and cost-effective way to produce high-quality hydraulic components. The process offers several benefits, including high precision and accuracy, strong and durable parts, cost-effective production, and versatility.
Types of Hydraulic Equipment Casting
Hydraulic equipment casting is an important process that involves creating metal components for use in hydraulic systems. There are several different types of hydraulic equipment casting, each with its own unique characteristics and applications.
Die Casting
Die casting is a popular type of hydraulic equipment casting that involves injecting molten metal into a mold under high pressure. This process is typically used to produce small to medium-sized parts with complex shapes and tight tolerances. Die casting is commonly used in the production of hydraulic valve bodies, pump housings, and other components.
Investment Casting
Investment casting, also known as lost-wax casting, is a process that involves creating a wax pattern of the desired part and then coating it in a ceramic shell. Once the shell has hardened, the wax is melted out and replaced with molten metal. Investment casting is a highly precise process that can be used to create complex shapes and intricate details. It is commonly used in the production of hydraulic pump impellers, valve bodies, and other components.
Sand Casting
Sand casting is a process that involves creating a mold from a mixture of sand and a binder material. The mold is then filled with molten metal and allowed to cool and solidify. Sand casting is a versatile process that can be used to produce parts of varying sizes and shapes. It is commonly used in the production of hydraulic cylinder heads, blocks, and other components.
Continuous Casting
Continuous casting is a process that involves pouring molten metal into a mold that is continuously moving through a cooling system. This process is typically used to produce long, uniform shapes such as bars or tubes. Continuous casting is commonly used in the production of hydraulic piston rods, tubes, and other components.
Overall, each type of hydraulic equipment casting has its own unique advantages and disadvantages. Manufacturers must carefully consider the requirements of their specific application when selecting a casting process.
Process of Hydraulic Equipment Casting
Hydraulic equipment casting is a manufacturing process that involves the production of hydraulic system components using metal casting. The process involves the use of molten metal that is poured into a mold to create the desired shape of the hydraulic component.
The process of hydraulic equipment casting begins with the creation of a mold. The mold is made using sand, ceramic, or other materials that can withstand high temperatures and pressure. The mold is designed to create the desired shape of the hydraulic component.
Once the mold is ready, the molten metal is poured into the mold. The metal is heated to a high temperature to ensure that it is in a molten state. The molten metal is then poured into the mold using a ladle or other pouring equipment.
After the metal is poured into the mold, it is left to cool and solidify. The cooling process may take several hours or even days, depending on the size and complexity of the hydraulic component.
Once the metal has cooled and solidified, the mold is removed, and the hydraulic component is cleaned and finished. The finishing process may involve sandblasting, polishing, or other techniques to ensure that the component is smooth and free of any defects.
Hydraulic equipment casting can produce a wide range of hydraulic system components, including pump housings, valve bodies, and cylinder heads. The process is widely used in the manufacturing of hydraulic equipment due to its ability to produce complex shapes and high-quality components.
Overall, hydraulic equipment casting is a complex process that requires precision and expertise to produce high-quality hydraulic components. It is a critical process in the manufacturing of hydraulic equipment and is used extensively in industries such as agriculture, construction, and mining.
Materials Used in Hydraulic Equipment Casting
Hydraulic equipment casting is a complex process that requires the use of high-quality materials to ensure the durability and performance of the final product. The materials used in hydraulic equipment casting are chosen based on their mechanical properties, chemical composition, and suitability for the specific application.
One of the most commonly used materials in hydraulic equipment casting is ductile iron. Ductile iron is a type of cast iron that is known for its high strength, toughness, and ductility. It is an ideal material for hydraulic equipment casting because it can withstand high pressure and is resistant to wear and corrosion.
Another material that is frequently used in hydraulic equipment casting is steel. Steel is a versatile material that can be alloyed with other metals to improve its strength and durability. It is often used to make hydraulic pump bodies, valve housings, and other components that require high strength and resistance to wear.
In addition to ductile iron and steel, other materials used in hydraulic equipment casting include aluminum, magnesium, and brass. Aluminum is a lightweight material that is often used to make hydraulic pump housings and other components that require high strength and corrosion resistance. Magnesium is also lightweight and is often used to make hydraulic valve bodies and other components that require high strength and resistance to temperature changes. Brass is a copper alloy that is often used to make hydraulic fittings and other components that require high corrosion resistance and good conductivity.
Overall, the materials used in hydraulic equipment casting play a crucial role in determining the durability and performance of the final product. Manufacturers must carefully choose the right materials based on the specific application and performance requirements of the hydraulic equipment.
Quality Control in Hydraulic Equipment Casting
When it comes to hydraulic equipment casting, quality control is essential to ensure that the parts produced meet the required specifications and standards. The casting process involves various stages, and each stage must be monitored to ensure that the final product is of high quality.
One of the critical aspects of quality control in hydraulic equipment casting is the inspection of raw materials. The quality of the raw materials used in the casting process can significantly affect the quality of the final product. Therefore, it is crucial to inspect the raw materials thoroughly before they are used in the casting process.
During the casting process, it is essential to monitor the temperature and pressure to ensure that the casting is formed correctly. Any deviation from the required temperature or pressure can result in defects in the final product.
After the casting is formed, it undergoes various finishing processes, including grinding, polishing, and painting. Each of these processes must be monitored to ensure that the final product meets the required specifications.
In addition to monitoring the various stages of the casting process, it is also essential to conduct final inspections to ensure that the final product meets the required standards. The final inspection may involve various tests, including pressure testing, leak testing, and dimensional inspection.
In conclusion, quality control is a crucial aspect of hydraulic equipment casting. By monitoring each stage of the casting process and conducting final inspections, manufacturers can ensure that the final product meets the required specifications and standards.
Applications of Hydraulic Equipment Casting
Hydraulic equipment casting finds its applications in various industries due to its durability and strength. Here are some of the applications of hydraulic equipment casting:
1. Metallurgical Industry
Hydraulic technology is widely used in the metallurgical industry for heavy, large, and very large equipment. Casting hydraulic systems are used in rolling mills and continuous casting hydraulic systems. Hydraulic equipment casting is also used in the production of hydraulic cylinders and hydraulic pumps.
2. Military Industry
In the military industry, hydraulic technology is used for high-speed response scenarios such as aircraft rudder control, ship rudder control, and high-speed response follow-up. Hydraulic equipment casting is used in the production of components such as hydraulic motors, hydraulic valves, and hydraulic pumps.
3. Manufacturing Industry
Hydraulic technology is used in the manufacturing industry for repetitive movement in machinery and tools. Hydraulic systems utilize fluid as a powering medium. Hydraulic equipment casting is used in the production of hydraulic cylinders, hydraulic pumps, and hydraulic motors.
4. Construction Industry
Hydraulic technology is used in the construction industry for heavy equipment such as excavators, bulldozers, and cranes. Hydraulic equipment casting is used in the production of hydraulic cylinders, hydraulic pumps, and hydraulic motors.
5. Agriculture Industry
In the agriculture industry, hydraulic technology is used for heavy equipment such as tractors and harvesters. Hydraulic equipment casting is used in the production of hydraulic cylinders, hydraulic pumps, and hydraulic motors.
Overall, hydraulic equipment casting is an essential part of many industries due to its strength and durability. It is used in the production of various components such as hydraulic cylinders, hydraulic pumps, and hydraulic motors.
Maintenance of Hydraulic Equipment Casting
Hydraulic equipment casting is an essential process in the manufacturing industry, and it requires regular maintenance to ensure optimal performance and longevity. Proper maintenance of hydraulic equipment casting involves regular inspection, cleaning, and replacement of worn-out parts.
One of the critical components of hydraulic equipment casting is the hydraulic system. The hydraulic system consists of several components such as pumps, motors, tanks, sumps, and hydraulic lines, hose assemblies, and pipes. Each component requires specific maintenance to ensure optimal performance.
To maintain the hydraulic system, it is essential to follow the manufacturer’s instructions for oil maintenance. The hydraulic oil needs to remain clean and free of any contaminants. Regular oil checks and replacement after every 1,000 hours of work are recommended.
Periodic maintenance of plant and equipment is also necessary to ensure optimal performance. Maintenance should be done from time to time, not only at the time of any breakdown. This will not only help avoid delay penalties and shutdown costs but also help upkeep the foundry’s good position in front of clients.
It is crucial to inspect and maintain the hydraulic lines, hose assemblies, and pipes regularly. Any leaks or damage can cause a significant reduction in hydraulic system performance. Regular inspection and replacement of worn-out parts are recommended.
In conclusion, proper maintenance of hydraulic equipment casting is crucial to ensure optimal performance and longevity. Regular inspection, cleaning, and replacement of worn-out parts are necessary to maintain the hydraulic system’s optimal performance. Following the manufacturer’s instructions for oil maintenance and periodic maintenance of plant and equipment are also essential.